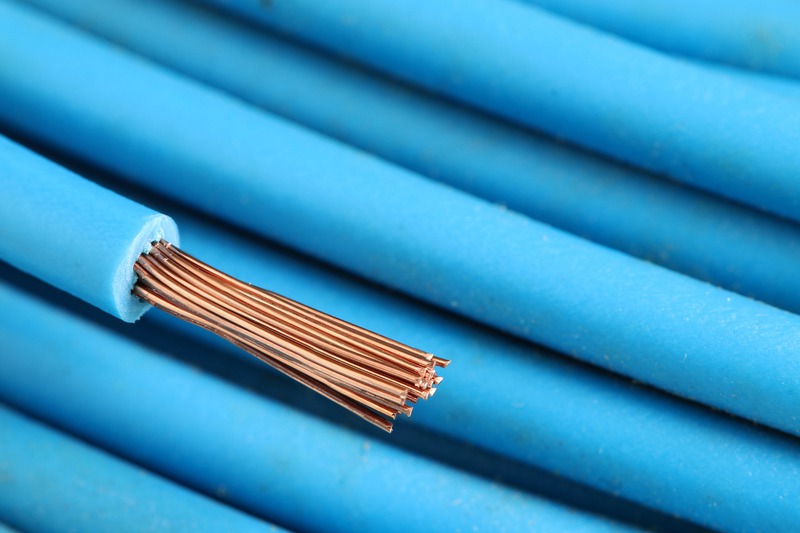
What Are the Best Practices for Sourcing High-Quality Wire?
When sourcing high-quality wire, prioritize understanding the specifications required for your project, such as gauge, material, and coating. Choose reputable suppliers known for reliability and quality assurance certifications. Check for consistent insulation and durability, ensuring it meets safety standards. Consider the wire’s flexibility and resistance to environmental factors like moisture or heat. Reading reviews and seeking expert recommendations can provide additional insights into performance. Balance cost with value, prioritizing long-term reliability over short-term savings. This careful consideration ensures your projects stand the test of time and function optimally.
Understanding Your Requirements
Before starting the sourcing process for wire, clearly define your needs. Determine what the wire will be used for, as this guides decisions on material, diameter, and flexibility. Understanding the application’s demands ensures you choose the right type of wire, whether it’s for electrical, structural, or mechanical purposes. Consider factors like conductivity, strength, and environmental resistance. By knowing your specific requirements, you streamline the selection process, ensuring efficiency and effectiveness in your final product or project.
Identify the Wire Specifications
-
Material: Are you looking for copper, aluminum, or steel? Each has unique properties and is suitable for different applications.
-
Diameter: The thickness of the wire matters significantly, influencing its conductivity and strength.
-
Insulation: Depending on the environment, you might need specific insulating materials to prevent accidents or degradation.
Researching Wire Manufacturers
Finding a reliable manufacturer is crucial. Here are some tips to get you started:
Examine the Manufacturer’s Reputation
-
Seek out reviews from previous customers to gauge satisfaction with the wire quality and company service.
-
Look for any certifications that can indicate industry standards and quality assurance.
Visit Manufacturing Facilities
Visit the manufacturing site to see the processes firsthand. This will give you a feel for their quality control and production capabilities.
Testing for Quality
Even after choosing a supplier, conducting your tests is wise. Here’s what you can do:
Understand Quality Assurance Practices
-
Ask about their testing processes—do they conduct tensile strength tests, conductivity tests, or corrosion resistance checks?
-
Inquire about their return policies if the wire does not meet your specifications.
Request Samples
Ask for samples before making a large purchase. Evaluate them under your specific conditions to ensure they meet your needs.
Evaluating Environmental Conditions
Consider where and how the wire will be used. Factors like temperature, humidity, and exposure to chemicals can affect the choice of wire.
Selecting the Right Insulation
-
UV-resistant insulation might be necessary for outdoor use.
-
If used around chemicals, ensure the insulation is resistant to potential reactions.
Negotiating with Suppliers
Once you’ve narrowed your choices, effective negotiation can secure the best deal. Here’s how:
-
Communicate Your Needs Clearly: Clearly articulate what you’re looking for in terms of specifications and quantities. This transparency can lead to better recommendations and pricing.
-
Discuss Long-Term Collaborations: Building a solid relationship can sometimes yield better discounts or priority service. This is particularly true if you foresee regular orders.
Focusing on Sustainability
With growing concern for the environment, consider the sustainability of your choices.
Look for Eco-Friendly Options
-
Consider recycled materials or options that reduce environmental impact.
-
Ensure the supplier has sustainable practices.
For those focused on cutting-edge technologies, fine wire drawing can offer precision and efficiency in wire production. This technique ensures high-quality and economical solutions, especially for intricate applications.
Quality and Cost Alignment
Balancing quality and cost is essential in sourcing. Opting for the cheapest option can lead to higher expenses later, due to issues like defects or replacements. It’s important to select a solution that fits your budget while maintaining reasonable quality standards. This approach minimizes long-term risks and ensures better value. By carefully assessing suppliers and products, you can find a middle ground that supports both financial efficiency and product reliability, ultimately aligning with your business needs and goals.
Leveraging Local Expertise
Consider working with a wire manufacturing company in Fort Wayne, IN or similar locales known for expertise in the wire industry. These manufacturers may offer localized solutions and insights particular to your needs.
Benefits of Local Suppliers
-
Faster turnaround times due to proximity.
-
Potential for in-person meetings and discussions.
If your project requirements include specific alloys, seeking expertise in alloy manufacturing Fort Wayne, IN, might lead you to discover innovative and customized solutions tailored to your needs.
Planning for Future Needs
Always consider your future requirements alongside your current needs.
Scalability
-
Does the supplier have the capacity to scale production up or down as needed?
-
Can they adapt to new technological advancements or changes in demand?
Final Thoughts
Sourcing high-quality wire starts with identifying your specific needs, such as material type and wire gauge. Research reliable manufacturers by reading reviews and checking certifications. Test wire samples for quality and durability to ensure they meet standards. Consider long-term partnerships with suppliers for consistent quality and better pricing. Communication with suppliers about your requirements is crucial. By following these steps, you can select the best wire for your project, ensuring efficiency and reliability. Focusing on quality and relationships helps build successful outcomes.